ASTM A105 Forge Carbon Steel Material Specification
ASTM A105 is the most commonly used carbon steel material grade that used to manufacture forge piping components such as flange and forged fittings of small diameter piping. This carbon steel material grade is used for ambient- and higher-temperature service in pressure systems.
Some of the components that are made by ASTM A105 are listed below.
- Flanges
- Valve Body
- Forged Fittings such as Elbow, Tee, Coupling, etc.
- Pressure vessel forge components such as a self-reinforced nozzle, nozzle neck, etc.
- As designed by Purchasers
However, there is a limitation on the use of this standard. The weight of the forging made by A105 material should not exceed 4540 Kgs. For forging heavier than 4540 Kgs are made by using ASTM A266.
ASTM A105 Material Properties
Only fully killed carbon steel material is used for forging. This material can be in the shape of a bar or in the shape of the ingot to meet various forging requirements. See the image below.
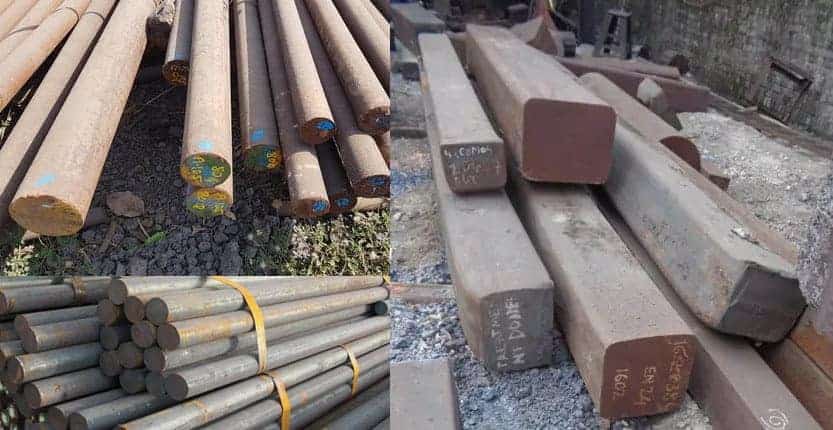
This bar is then cut into the required length to do forging of a flange. See the video below to understand the flange forging process. You can see the closed die flange manufacturing process.
In the image below, you can see various ASTM A105 products such as a flange, fittings, nozzle neck, self-reinforced branches that used in industries such as oil and gas, petrochemical, power plant, etc.
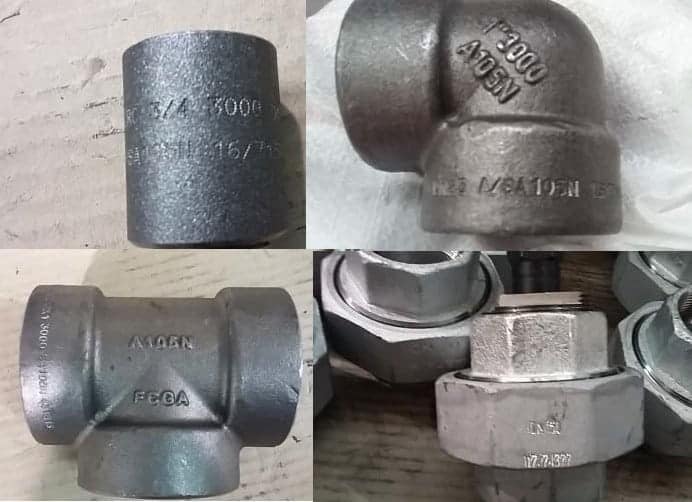
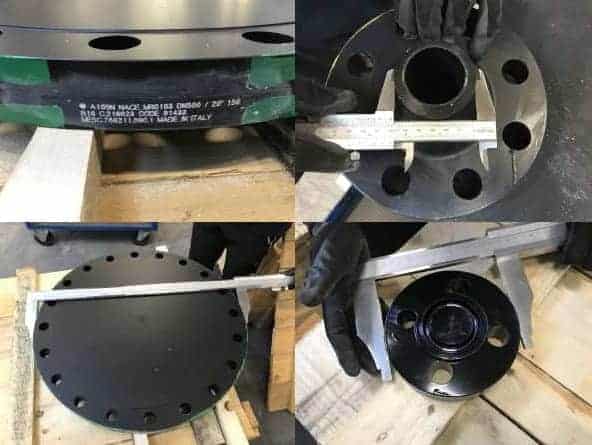
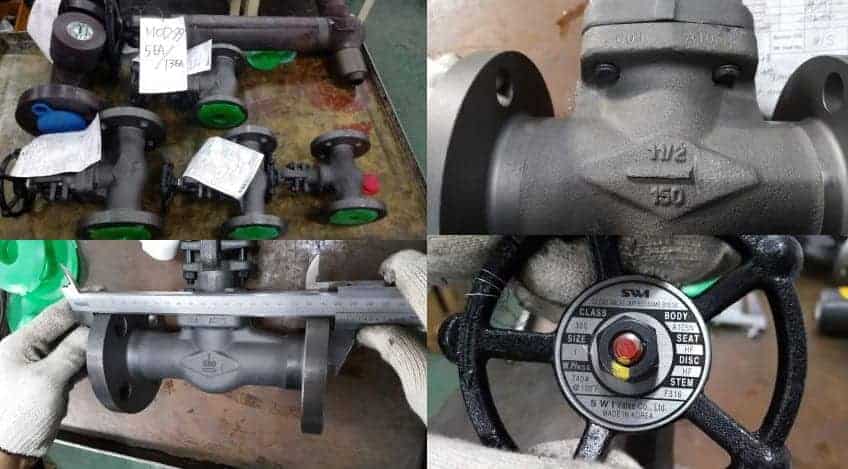
Heat Treatment is a must for all the product manufactured with ASTM A105 except following;
- Flange Class 150 and Class 300
- Piping component NPS 4 and below with pressure class 300 or less
Following Hear Treatment method you can use;
- Annealing – In Annealing, the material shall be uniformly reheated to a temperature above the transformation range and, after holding for a sufficient time at this temperature, cooled slowly to a temperature below the transformation range.
- Normalizing – In Normalizing, the material is uniformly reheated to a temperature above the transformation range, and subsequently, cooled in the air at room temperature.
- Normalizing and tempering
- Quenching and tempering – In this method, the material is first fully austenitized and then quenched immediately in a suitable liquid medium. The quenched fittings again reheated to a minimum temperature of 590°C of 1100°F and then cooled in still air.
Chemical Composition of ASTM A105 Materials
Refer table below for the chemical composition;
Material | Percentage % |
---|---|
Carbon | 0.35 max |
Manganese | 0.60–1.05 |
Phosphorus | 0.035 max |
Sulfur | 0.040 max |
Silicon | 0.10–0.35 |
Copper | 0.40 max |
Nickel | 0.40 max |
Chromium | 0.30 max |
Molybdenum | 0.12 max |
Vanadium | 0.08 max |
Columbium | 0.02 max |
The sum of copper, nickel, chromium, molybdenum and vanadium shall not exceed 1.00 %. | |
The sum of chromium and molybdenum shall not exceed 0.32 %. | |
For each reduction of 0.01 % below the specified carbon maximum (0.35 %), an increase of 0.06 % manganese above the specified maximum (1.05 %) will be permitted up to a maximum of 1.35 %. |
Mechanical Properties of ASTM A105 Materials
To confirm the strength and ductility of the material, tensile tests and hardness tests are performed on the specimen that cut out from the sample that heat-treated along with the final product. In the video below, you can see how the tensile test is performed on the test specimen.
Acceptable values of mechanical testing results are given in the table below.
Tensile Strength min. | Yield Strength min. | Elongation min. | Reduction of Area, min. | Hardness | ||
---|---|---|---|---|---|---|
MPa | ksi | MPa | ksi | % | % | HB |
485 | 70 | 250 | 36 | 22 | 30 | 137-187 |
Number of Sample Testing requirements
One tension test shall be made for each heat of as-forged components.
One test specimen per heat number if the entire batch is heat-treated in a single lot. Otherwise, each batch of heat treatment shell has one sample of test specimens per heat number.